The impact of boiler shape on spirit quality during distillation
Gert BosmanHave you ever thought about the impact that your boiler configuration has on the qualilty of the spirits you distill?
Let's compare two different boilers. One fat and short (A) and the other tall and thin (B).
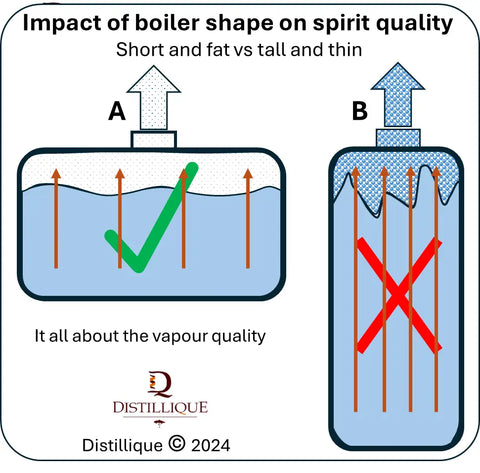
Lets assume they have both the same mash (i.e. at 20%abv for the purpose of calculations), the same volume of mash (i.e. 100L), the same heat input (i.e. 4kW without external heat losses) and they are boiling the mash to be distilled in a potstill or column still. Lets also assume both are heated from the bottom (either a flame or a heating element) and that there are no reflux running back into the boilers.
On both boilers vapour bubbles will form at the bottom when the heat is supplied at the bottom. As both boilers have the same energy input, the volume of bubbles will be approximately be same (Let's not split hairs about the tiny pressure difference at the bottom). As the vapour bubbles rise to the top, two main things happen with the bubbles:
1. Initially, at the starft of the boil, the bubbles will become rapidly smaller as they riseand give of heat to the surrounding (colder) mash (that is not boiling yet). The closer we get to all liquid boiling, the less this will effect the bubble size and the bubbles at the surface, will be very much the same size as when they were greated at the bottom of the mash. This means that when the whole mash is boiling, a lot of relative large bubbles will break through the surface.
2. As the bubbles rise through the mash, they will pick up speed and the taller the boiler (boiler B), the faster the bubbles will go when they break through the surface of the mash.
It is already clear that the mash's surface in boiler B will be much more violent with droplets splashing all over, than that of boiler A.
Also: The surface area of the mash in boiler B is much smaller than in boiler A and therefor boiler A has a higher "density of bubbles bursting through the surface per square metre surface area". This greatly contributes to the "violence" of the boil.
Both the speed of the bubbles,, when it break through the surface of the mash, and the bubble density (per sq meter mash surface area) cause a much more "violent boil" in boiler B than in boiler A.
This violent boil in boiler B causes tiny mash droplets being propelled into the space above the boiling liquid. We call this the "boiling kinetic effect" (i.e. little mash droplets in the air and gas, rather than only vapour/gas in the space.)
The closer we get to all liquid boiling, the bigger the bubbles that burst through the surface and the bigger the kinetic effect, especially in boiler B.
If the surface area of boiler A is large enough, the rising bubbles will have very little, or with neglible, kinetic effect and the vapour/gas above the mash will be "pure vapour" without any droplets of mash in it.
With no kinetic effect, we will stil have a convection effect in the mash itself. which will result in a slow rolling boil. This is what we want to produce high quality spirits as this allows us to trake better cuts and identity various fractions much better during the distilling process.
A rolling boil looks like a calm sea surface with waves (Boiler A) goinbg up and down but without any breakers, whereas Boiler B's liquid surface will look like the sea surface in a violent storm!
To quantify the difference between boiler A and B:
Description | Boiler A | Boiler B | Units |
Heat input | 4 | 4 | kW |
Boiler mash volume | 100 | 100 | L |
Boiler diameter | 500 | 300 | mm |
Mash height | 509 | 1412 | mm |
Mash flat surface area | 0.196 | 0.071 | m^2 |
Vapour volume flow rate | 1.96 | 1.96 | L/s |
Vapour flow rate per square meter surface area | 10.0 (V500) | 27.7 (V300) | L/s/m^2 |
Kinetic effect index (Vx/V500-1) | 0 | 1.8 |
From the above it shows that Boiler B will have a vapour/gas mixture with mash droplets in the headspace of the boiler (due to its high kinetic index) and this mixture will enter the distilling column or lynn's arm of a potstill. This is problematic because these droplets are actual droplets of mash and has not been distilled (vapourised and then condensed) at all.
In short: Rather select a short and fat boiler and boil with a rolling boil to prevent some of your mash finding its way into your spirits.
Tall thin boilers does not do your spirits a favour.
Note: it is worthwhile to note that the kinetic effect can be slightly reduced by lengthening the headspace in a tall boiler but only within limits as the flow of steam/gas/vapour up the boiler can actually carry some of these droplets into your swan's neck.
With a plate of column still, the kinetic effect's impact is reduced almost equally to removing one or to plates in the column. this means a 6 plate column will work as a 4 or 5 plate column, depending on how strong the kinetic effects carries the mash droplets into the column.